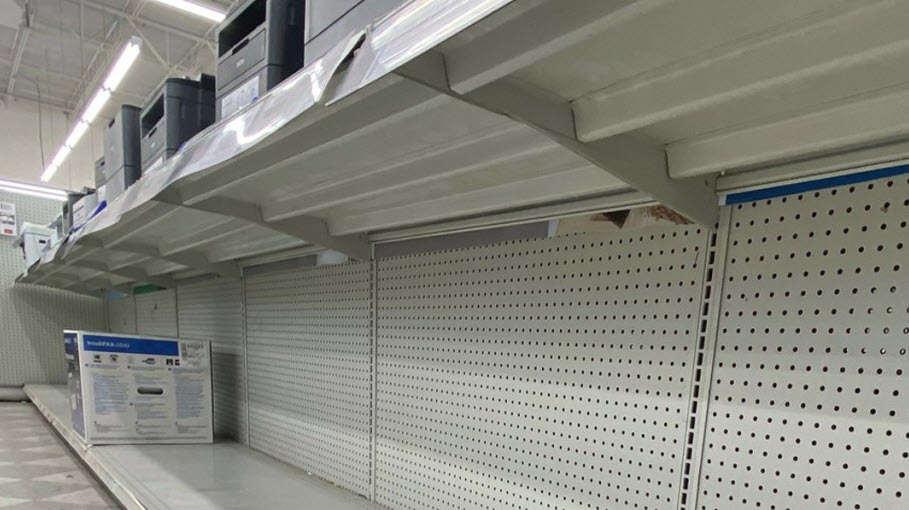
The present chip shortage has made plenty of headlines in the mainstream press. Where this is most acutely felt is in the printed circuit board design space. Components (a.k.a chips) are electronic functional elements that make up a circuit. They come together on a medium known as the Printed Circuit Board (PCB). These are the green boards you find in your electronic equipment.
With the chip shortage, designers are scrambling to design products that can be produced in quantity and on time. It is true for existing product lines as well as new products. The shortage is forcing many companies to seek alternate components for their existing designs. Maybe 10 companies make similar components like resistors and capacitors; thereby, providing ample choices to procure the necessary component. However, part substitution is far more problematic for components like processors, FPGAs, power management integrated circuits, and other function-dedicated components.
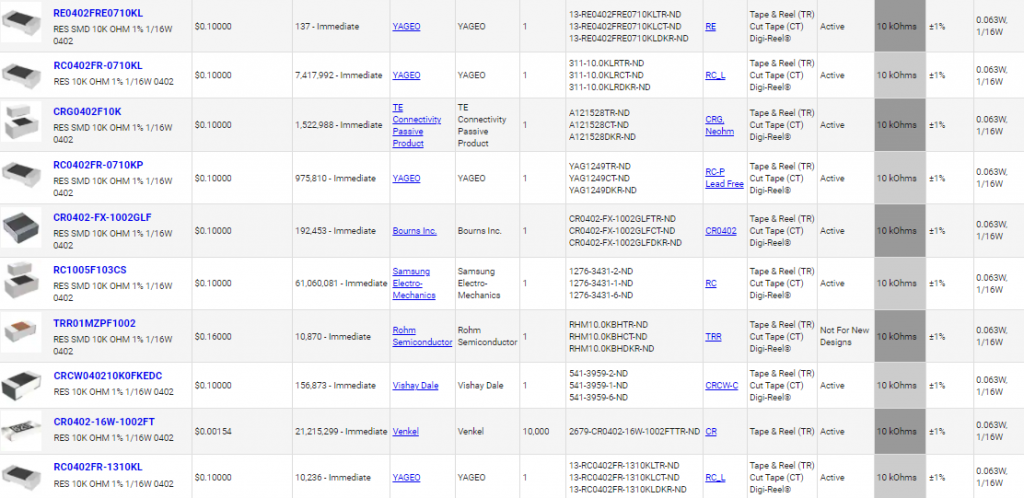
When a designer is creating an electronic device, they choose components that are available on the market. This practice has been the norm long before the chip shortage. Given the complexity of many of these devices, the selection of such components is made with careful consideration such as lead times, price, prior experience with the product or the family of products, company reputation, and component characteristics such as value, temperature rating, tolerance, etc. The more functionality of a component, the more research and knowledge are needed.
What is different now is that the status of component availability can change overnight. Much of this has to do with indiscriminate hoarding of components, global material shortage, and supply chain disruptions.
In the past, a company’s purchasing and engineering departments have kept an arm’s distance between them. In some cases, the relationship between purchasing and engineering is less than civil. This shortage is forcing these two groups to unite.
Handoff to Purchasing

Before the chip shortage, the Bill Of Materials (BOM) needed to be handed to purchasing upon completing the schematic design. The layout of the PCB would commence with the understanding that purchasing may find issues. If issues were found, the schematic would be addressed, components would be corrected or added to the library, the design would be rereviewed, and the PCB layout would resume with the corrections. Though there was a negative hit on the schedule, no monetary investment was made to fabricate the board or assemble components onto the board.
The ability to hand off a BOM to purchasing upon completing the schematic design requires automation. This is only possible when every component in the design is properly declared in a library. The library must have consistent parametric information. When done correctly, the BOM builds itself as each component is placed on the schematic.
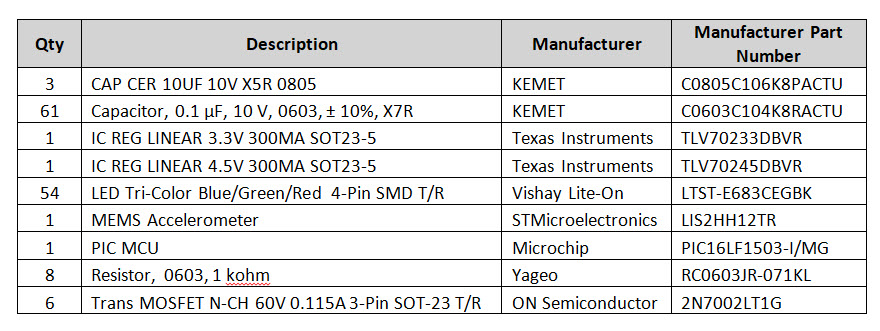
The keeping and maintenance of a component library sound logical, but many company libraries are in chaos or even nonexistent. The tech wreck of 2002 and the great recession of 2008 saw the dismissal of many component librarians and component engineers. The task of component creation for a design project fell on the designers. Though many designers would like to have a well-maintained library, it’s not their job function, nor are they trained for it. Their job is to create a product and meet the deadlines necessary to get that product to market. To keep with these deadlines, designers obtain libraries from 3rd parties or draw components as needed to keep the design moving forward. It should be noted that libraries from 3rd parties are not guaranteed nor vetted.
As a result, there is no automation to derive the BOM, and it must be created manually. More significantly, the BOM gets addressed after the PCB layout is complete.
Why so late in the design process? The designer does not have the time to deal with the BOM until the PCB layout is completed. The board is often sent to fabrication when the designer begins work on the BOM. That is when all the issues are unearthed, such as the End of Life (EOL), long lead times, and inflated costs, not to mention possible errors in the footprints since the components were not properly vetted. This situation was detrimental before the chip shortage and now practically guarantees a design that will not make it to market or will make it to market after a great deal of rework (and angst).
Even submitting a BOM when the schematics are complete may be too late with the chip shortage. The time between the start of the design and the handoff of the BOM can be weeks or even months, depending on the complexity of the design.
When does purchasing need to know? Under current circumstances, they need to investigate a component that the designer believes is viable for the design ASAP. We can conclude that, at minimum, a central library is necessary if one wants to bring a viable BOM to purchasing before layout. However, purchasing needs to know about component decisions as quickly as possible to handle procurement. This means that purchasing and engineering must have tighter interaction between their systems.
Unified Design and Purchasing Libraries
The thought of having the purchasing database and design library act as one is not new. Getting cooperation for this arrangement has not been easy. Purchasers do not want to deal with hypotheticals. They want a BOM that represents what the design needs. Therefore, before the chip shortage, handing the BOM to purchasing upon completing the schematic made the most sense.
From a system perspective, a separate component library and purchasing system has always been problematic. The information between the two systems is not in sync. In addition, the data being collected will be different. Though the designers are interested in parameters such as cost, or lead time, this is dynamic data that changes all the time. This is something that designers would not have time to update consistently. There is also data that the designer might like to know, but it adds more effort to create the components. This would be data such as RoHS, REACH, mineral conflict, and ITAR.
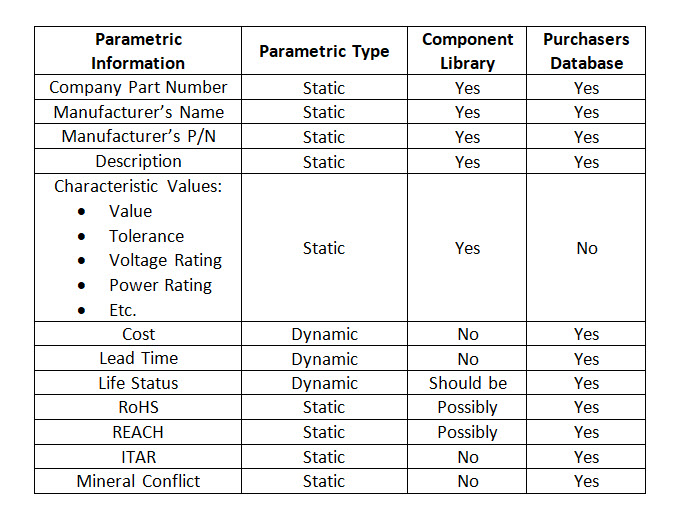
The component is first introduced into the component library. That component is used in a project. When the schematics are completed, the BOM is introduced to purchasing or an MRP (Material Requirements Planning) system.
Any status such as lead times, prices, or EOL issues is not automatically pushed back into the engineering component library. This information would be presented to the designer in the form of e-mails or sticky notes. It would be up to the designer to make such changes to the library. They will not update the library in most cases unless there is a fundamental issue with the component. As a result, there will always be a lack of synchronization between the purchaser’s database and the component library.
With the chip shortage, the integration of the purchasing database along with the component library becomes beneficial or maybe even critical to both parties. Having a component first introduced into the purchasing system and then propagated to the library gives the purchasers an early notification that the component may be used in a design. With services like IHS Markit and SiliconExpert, purchasing can not only check the availability, but it can also obtain the parametric data for the component. These services also offer statistical information to allow for better decision-making for the procurement of the components.
When the component is first introduced to the purchasing database and propagated to the component libraries, the synchronization issues are minimized. The purchasers and designers are now working in unison to ensure that the components being selected for the design can be procured. For the designers, having the purchasing system review a new component ensures that the parametric information is valid and it provides parametric information that they would not generally add to the component library on their own. If there is any automation to this process, dynamic data such as cost and lead time can be added to the component library.
In conclusion, the chip shortage is undoubtedly making the design process more difficult. By partnering with purchasing and investing in systems that allow for tighter integration between the purchasing database and the component libraries, designers can ensure that the components needed for the product can be or have been procured.
Nine Dot Connects provides library services, especially for Altium Designer. If you have questions about your libraries, please get in touch with us. There is no obligation, and we can guide you to a solution that works for your company.
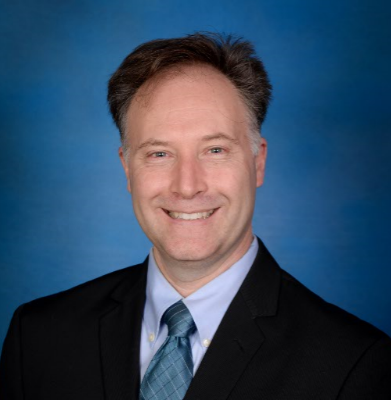